321 Stainless Steel Tubing
Another variant of the 304 standards, small diameter 321 stainless steel tubing (UNS designation UNS S32100) composition includes titanium which makes the resulting tubing stronger and more corrosion resistant at higher temperatures.
Small diameter 321 stainless steel tubing has substantially better resistance to intergranular corrosion which is corrosion that occurs in between the microstructure---between the grains of different elements that make up the alloy. 321 SS is, therefore, an important material option for tubing products with service cycles in the 800-1500º carbide precipitation range because the life of the product will be extended (relative to other grades of stainless steel).
321 SS Tubing Features & Applications
321 stainless steel tubing manufactured for high-temperature applications exhibits excellent resistance to fatigue and cracking, making it ideal for applications including:
- Metal O-ring products
- Select aerospace applications
- Exhaust manifolds
- Oil and gas/refinery applications
- Processing equipment for high-temperature chemicals
- Many other high-temperature service applications
Like our other welded and drawn products, small diameter 321 SS tubing is welded from strip stock, plug drawn in coil form, annealed as needed in order to meet customer temper requirements, and offered in straight lengths or coil form.
EXPLORE STAINLESS STEEL TUBING SIZES
Learn more about the most popular and widely used dimensions in the industry.

Short Mill Lead Times
Pre-welded work-in-process inventory, a responsive & resourceful staff, a vast range of tooling and quick changeover equipment enables quick delivery.

Made in the USA
Tubing is produced domestically and DFARS compliant products are available. Rely on USA manufactured tubing for critical applications and avoid quality problems or logistics delays with foreign firms.
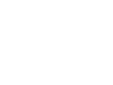
All Manufacturing in House
Welding, tube drawing, heat treating, straightening and related processes are all performed under one roof. This approach reduces opportunities for delays and ensures processes are well controlled.

Quality
Multi point inspection throughout the manufacturing processes detects and contains defects. Non-contact measurement devices and automated vision inspection systems used in-line during production.