316 LVM Stainless Steel Hypodermic Tubing
316 LVM (UNS designation S31673) is a stainless steel grade melted in a vacuum furnace (vacuum arc remelted, or VAR) to reduce as many impurities as possible and the result is high purity and clean alloy with good homogeneity and uniform chemistry. 316 LVM is typically used for medical applications. 316LVM stainless steel tubing is a derivative of the 316 stainless steel grade and the “L” in the designation indicates it has a low carbon content.
Aside from improved purity and thus better resistance to corrosion for critical applications, 316LVM otherwise shares many of the same characteristics as standard 316 tubing. It can be cold worked to a hard temper (or can be offered in an intermediate or annealed temper). 316 LVM tube is offered in coil or straight lengths and is easily machinable via grinding, turning, and milling or can be fabricated via EDM, ECM, laser, or other techniques. Frequently, it is ordered using the ASTM F138 chemistry specification.
316 LVM is more expensive than 316 or 316 L tubing due to high minimum material costs from suppliers and the added cost from the vacuum melting process.
316 LVM Tubing Features & Applications
The most common application for small diameter 316LVM stainless steel hypo tubing is typically medical, where surgical grade tubing is necessary. Applications include:
- Medical device instruments
- Surgical devices, especially those for reusable applications
EXPLORE STAINLESS STEEL TUBING SIZES
Learn more about the most popular and widely used dimensions in the industry.

Short Mill Lead Times
Pre-welded work-in-process inventory, a responsive & resourceful staff, a vast range of tooling and quick changeover equipment enables quick delivery.

Made in the USA
Tubing is produced domestically and DFARS compliant products are available. Rely on USA manufactured tubing for critical applications and avoid quality problems or logistics delays with foreign firms.
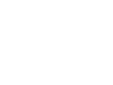
All Manufacturing in House
Welding, tube drawing, heat treating, straightening and related processes are all performed under one roof. This approach reduces opportunities for delays and ensures processes are well controlled.

Quality
Multi point inspection throughout the manufacturing processes detects and contains defects. Non-contact measurement devices and automated vision inspection systems used in-line during production.